CR3 Group’s brand-new identity reflects a strategic emphasis on sustainability and clean energy. Group Business Development Manager, David Young, tells us more.
RE-ENERGISE AND REBRAND
Energy efficiency, engineering excellence, sustainable solutions.
The three core skills of CR3 Group (CR3) are embodied in the energy engineering solutions and maintenance provider’s latest rebrand.
As well as signifying the third iteration of the group’s name and highlighting three decades of operations, the new CR3 brand identity comes as customers operating in a variety of industries pursue continuous improvements in energy efficiency and decarbonisation.
Established in 1991, CR3 has continued to build on the group’s reputation for excellence in energy engineering solutions, while pursuing future opportunities in the transition to a low-carbon economy.
“2021 marked our 30th anniversary. Since we started out in Singapore, we have grown our business to service energy clients in 18 Asian countries, with permanent facilities in Thailand, India, Malaysia, and Singapore,” opens David Young, CR3’s Group Business Development Manager.
To better serve clients, the new CR3 brand is committed to expanding further beyond these traditional Asian markets with its energy engineering solutions.
“As we continue to grow, we will continue developing our people, technology, and systems to provide safer, faster, and more efficient solutions.”
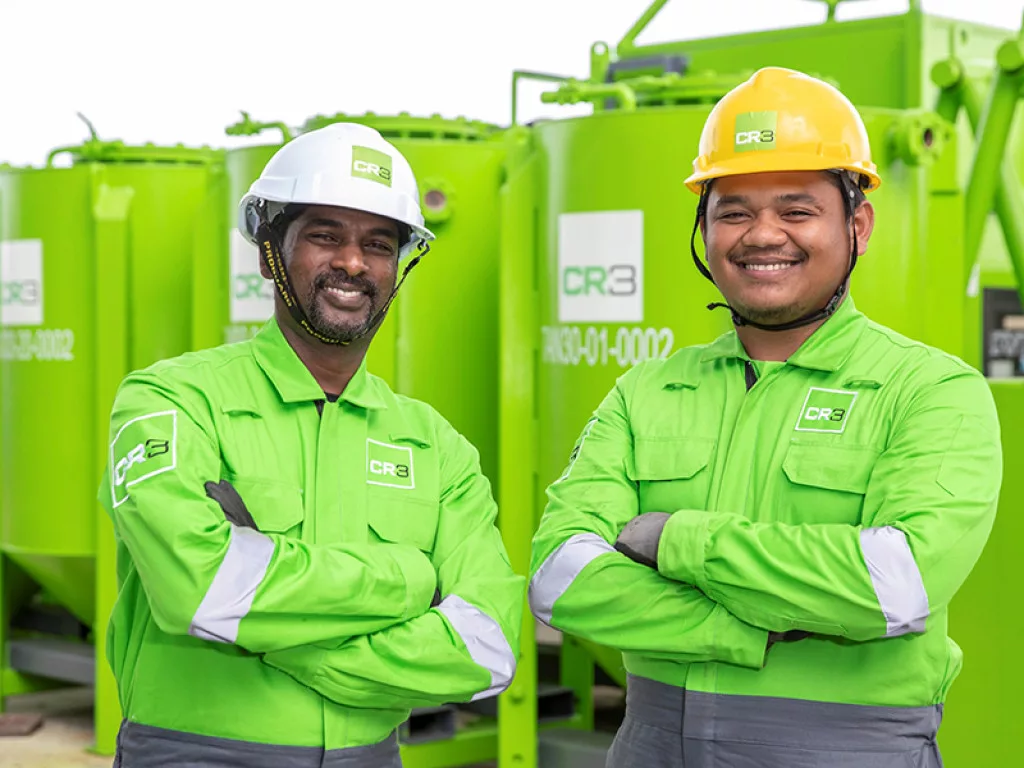
STAND-OUT IDENTITY
CR3’s vibrant new logo highlights the importance of sustainability to the energy market, and embodies its commitment to continuously developing and expanding the energy sector beyond Asia, as well as a greater focus on adding innovative and sustainable engineering solutions.
“Our visual identity will stand out in the energy landscape for our partners and customers. Our new website, logo, branding, tools and resources are precisely what CR3 needs to keep up with our future plans, and we will continue to offer comprehensive solutions with a more customer-centric approach,” emphasises Young.
The corporate name change is a significant milestone for CR3, as it offers a more focused message when it comes to providing energy-efficient solutions that meet today’s carbon challenges.
“CR3 is committed to reducing carbon emissions by 50 percent by 2030, and is targeting carbon neutrality by 2050,” he adds.
The company aims to do this by proactively exploring a number of initiatives including but not limited to using renewable energy to power its offices and workshops, transitioning to cleaner fuels for its machines, continuing to invest in energy-efficient equipment, and incorporating digital solutions to streamline business operations and reduce the need for travel.
“Our efforts towards this goal were given increased focus when we completed our latest greenhouse gas (GHG) assessment, which was an excellent way to identify and understand the largest source of GHG emissions within our organisation.
“We can expect further emissions reductions with several initiatives, including energy efficiency, electrification, and the rapid uptake of low-emission energy sources – particularly renewables – and reducing business travel,” Young continues.
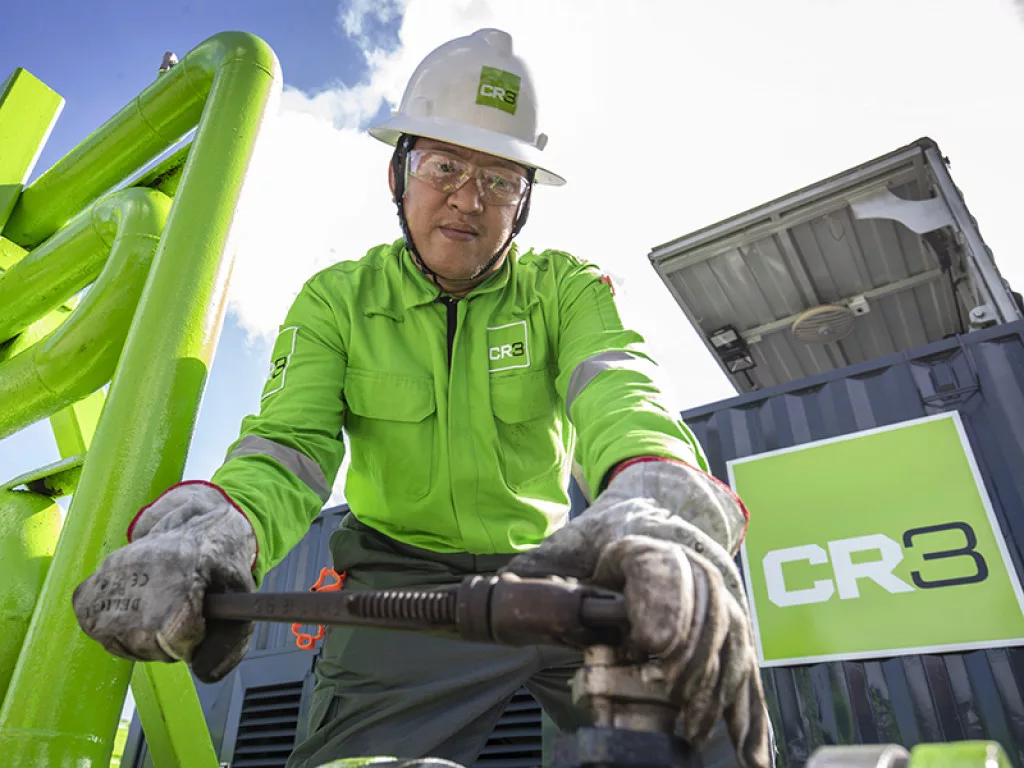
At sites across the business, the use of solar panels as an alternative source to power CR3’s offices and workshops is at the final review stage, while all new, large equipment purchased to support company operations will be powered by electricity where possible.
CR3 is also eliminating the use of single-use plastics, and will switch to more eco-friendly refrigerants such as R401A. “These initiatives are consistent with global industry standards, and we look forward to evaluating our improvements year-on-year,” Young tells us.
“Our early actions and market-driven sustainable solutions will reduce our carbon emissions footprint and increase our environmental transparency for all our clients and partners to benefit.”
Working collaboratively with all stakeholders, including customers, suppliers, partners and staff, to deliver a fair, safe and sustainable future, CR3 acknowledges the need for serious, urgent and immediate action to tackle climate change.
CR3 recently received the Green Industry Level 4 (Green Culture) award from the Department of Industrial Works and Ministry of Industry in Thailand, in recognition of its commitment to environmentally friendly and sustainable operations.
The company follows the principles of sustainable development and continuous improvement, aiming to create business growth while promoting socio-economic and environmental sustainability.
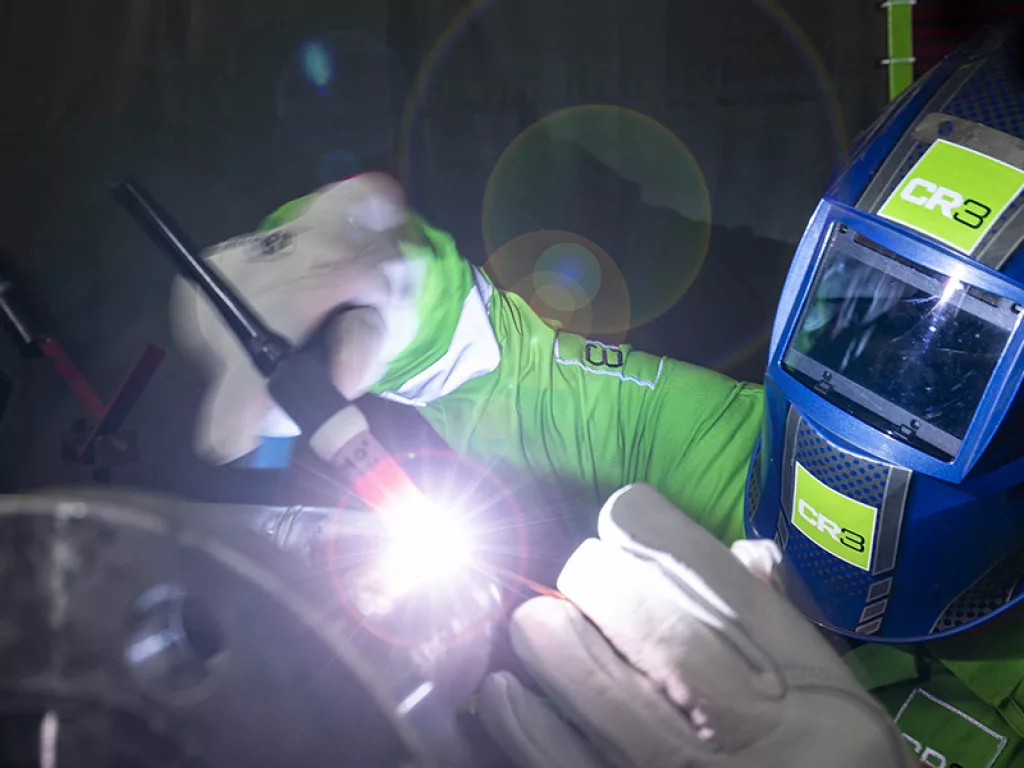
IMPROVEMENT AND INNOVATION
CR3 recognises the need for continuous improvement and innovation, specifically to improve safety, increase efficiency and productivity, and support the company’s sustainability aspirations.
“Our innovation programme is designed to work with all stakeholders and capture and develop new ideas by leveraging the business and social networks of all staff,” outlines Young.
“Our Innovation Champions are passionate about improving the way we work. They are open to new ideas and help to facilitate our innovation programme in each region.”
In addition to developing robotics for unloading catalysts and tank cleaning, CR3 has received ‘Zone 0’ certification for its remotely operated Rover platform, making it the only proven robotic solution for working in explosive environments. Rover represents the company’s family of remotely operated vehicles designed to significantly reduce or, in some cases, eliminate personnel entering confined spaces. One of the big advantages of Rover is that it does not require frequent breaks, unlike its human equivalent, which greatly reduces maintenance time.
“CR3 pride ourselves on maintaining an unblemished track record for quality and safety. Every technician is accredited under our confined space and inert entry training courses and our technicians will readily produce their training records for verification upon request. CR3’s lockable helmets incorporate a breathing mask and built-in headset for communicating with team members to ensure the safest experience under the toughest of conditions,” Young explains.
Another in-house innovation is CR3’s Advanced Wet Dumping (AWD) process, which combines drilling with high-pressure water jetting technology to unload heavily fused catalysts faster and more safely than manual methods by eliminating the need for nitrogen, reducing cool-down times, and shortening overall schedules by at least 50 percent on average. Integral to the design is a closed loop waste-water treatment system that significantly decreases the amount of fresh plant water usage by over 80 percent compared to one-time operation. This waste-water treatment system can be used in a wide range of industrial applications, further demonstrating the company’s desire to conserve precious resources and be more sustainable in everything it does.
Innovation is an excellent growth enabler, and as the company targets ever larger maintenance contracts and turnarounds, CR3 is developing new high-pressure water jetting equipment that will further improve efficiencies by 40 percent. The autonomous nature of this advanced technology will also increase productivity, as higher pressures and flows can be used, and the heat exchangers will run longer than traditional cleaning methods. “We probably have the largest fleet of specialised high-pressure water jetting equipment in the market and are continuously looking for ways to improve performance while reducing our environmental impact by using cleaner fuels and sourcing more efficient engines to reduce emissions,” Young explains.
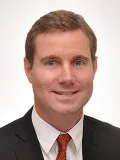
“Our visual identity will stand out in the energy landscape for our partners and customers”
David Young, Group Business Development Manager, CR3 Group
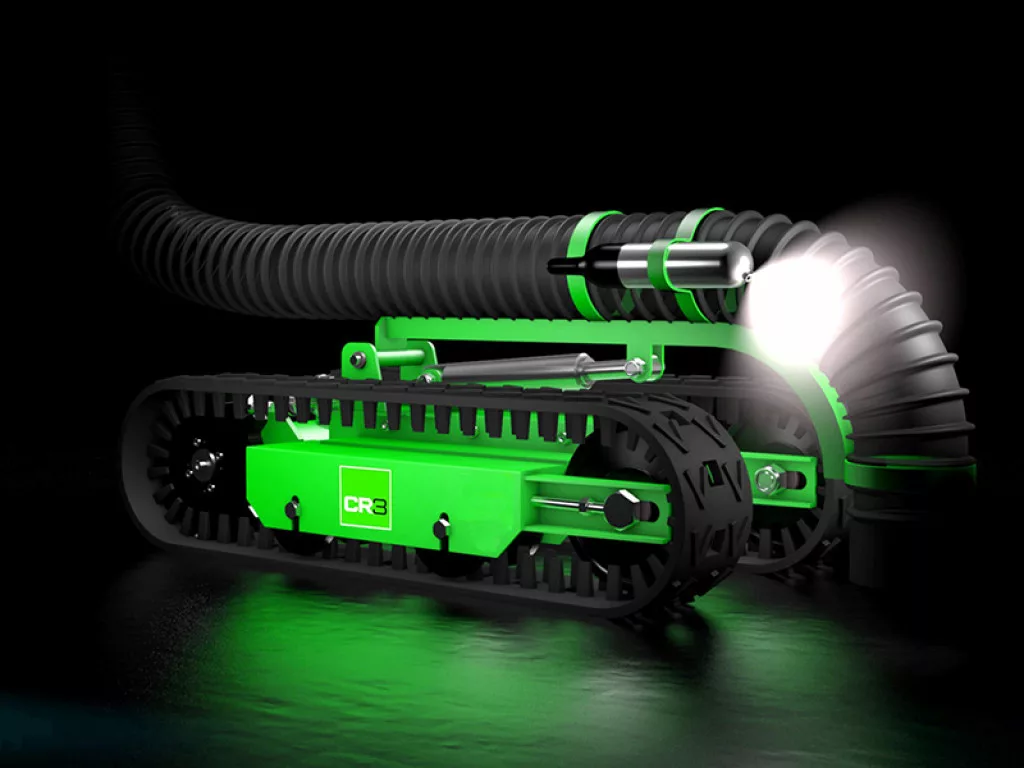
BEST-IN-CLASS PERFORMANCE
CR3 is busy preparing for a major turnaround at a large integrated refinery and petrochemical complex in Southeast Asia.
Together with key technical partners, the company aims to achieve best-in-class performance while optimising the total cost and schedule for the client.
“In order to cope with the extremely large number of heat exchangers that require maintenance, we will be sourcing four additional high-pressure water pumps and six semi-automated exchanger cleaning units,” Young tells us.
“These additions to our fleet of specialised equipment will maximise our productivity and keep our operators safe.
“The turnaround will start in September and involve 1,800 professionals from multiple disciplines and a wide range of modern specialist equipment. This approach is necessary to ensure that all scope of work is completed safely within the timeframe expected by the client,” he continues.
CR3’s advanced automation technology for heat exchanger maintenance, along with its highly skilled staff and excellent project management, also recently facilitated a successful turnaround of a Vinyl Chlorine Monomer (VCM) unit at a petrochemical plant in Thailand.
By using its superior Internal Bundle Cleaning (IBC) technology, CR3 completed the heat exchanger work in a fraction of the time it takes with other conventional cleaning methods.
“In addition to our heat exchanger maintenance, the scope also includes column and vessel maintenance. Our comprehensive approach covers all aspects of column and tower internals, from inspection to installation, ensuring we deliver optimal safety, quality, and schedule efficiency,” acclaims Young, citing the client recognition of CR3’s outstanding work and leak-free start-up.
The company’s hydraulic drum tipper was also recently recognised at the WSH Innovation Awards by Singapore’s Workplace Safety and Health (WSH) Council. This catalyst handling innovation is capable of lifting up to four drums of different weights and sizes to deliver contents into loading hoppers or bulk bins safely and efficiently.
CR3’s automated four-drum tipper is a significantly safer solution, at least 20 percent faster than traditional methods of unloading drums, avoiding manual handling, working at heights, fatigue, and relying less on forklifts and cranes.
“The WSH Innovation Awards recognise work teams for their innovative solutions to improve health and safety standards in the workplace. This is our first year at this annual event and we are delighted to be recognised for our innovative solutions to improve the safety of catalyst handling,” Young smiles.
“CR3 is committed to reducing carbon emissions by 50 percent by 2030, and is targeting carbon neutrality by 2050”
David Young, Group Business Development Manager, CR3 Group
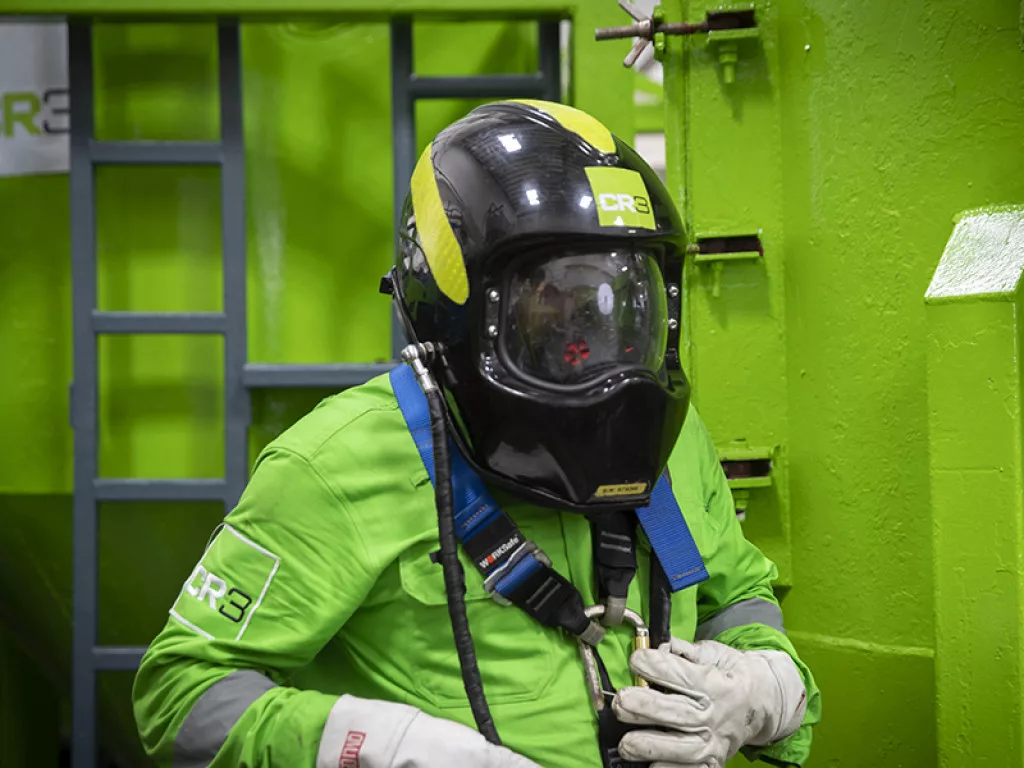
GROWTH AND INVESTMENT
CR3 is investing over MYR nine million in Malaysia after awarding several contracts, including the daily maintenance and turnaround services for an integrated refinery and petrochemical complex in Pengerang.
New automated cleaning equipment and a 125-tonne bundle puller for performing heat exchanger maintenance represent some of the recent additions to the CR3 fleet, to enhance safety and efficiency.
Further investments are being made in major equipment for a multi-year Atmospheric Residue Desulphurisation (ARDS) contract, which will utilise CR3’s AWD technology.
“AWD is proven to be safer, faster, and more reliable than conventional alternatives, enabling schedules to be guaranteed and delivering considerable cost savings,” says Young.
At the same facility in Malaysia, CR3 has been awarded a five-year contract for site-wide chemical decontamination services. The company’s world-class decontamination solution, along with its streamlined approach, minimises manual and mechanical cleaning and uses a lot less equipment than standard methods.
By tailoring the chemistries to different process units, CR3 typically uses at least 30 percent less chemistry than other traditional decontamination processes and provides easy access to all major equipment within 8 to 12 hours.
“The chemistry is exceptionally efficient yet safe, and free of volatile organic compounds, making it harmless to wastewater, resulting in significant savings in treatment and waste disposal costs,” Young shares.
“After decontamination is complete, you can confidently enter the process vessels for inspections and maintenance, including hot work, without the need for breathing apparatus and life-support equipment. We have engineered and applied chemistry to suit almost every process system in the refinery and petrochemical complex.”
CR3 is also proud to have secured a two-year initial routine maintenance service contract for a leading producer of petroleum products in Thailand.
Meanwhile, in India, CR3 is now hiring to support its new contract at the world’s largest refinery complex, following a five-year extension of its existing plant maintenance contract, in which the company has significantly reduced costs, improved safety, quality and productivity on site.
Over the last five years, CR3 has grown substantially in India, where it has invested more than USD seven million in new equipment and facilities to support projects and long-term contracts in the country.
“We would like to thank our loyal employees for their incredible commitment and dedication in supporting a permanent presence contract for a major Indian refinery. Our teams there have been executing several mini shutdowns under the difficult conditions during the COVID-19 period,” Young admires.
With a large number of employees also working continuously on customer sites in Malaysia, Thailand, Vietnam and the Philippines, Young is deeply grateful for the dedication and positive attitude of all CR3 employees.
“Our people work tirelessly to provide an essential service in challenging conditions; our respect goes out to these courageous individuals for their outstanding contributions.”
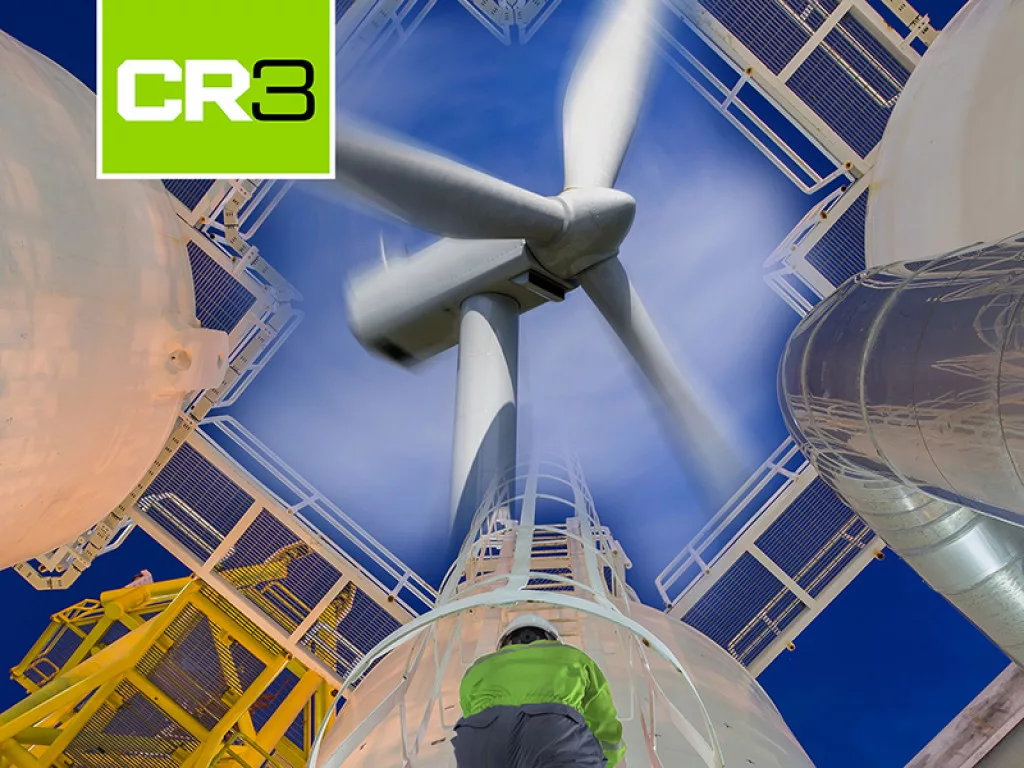